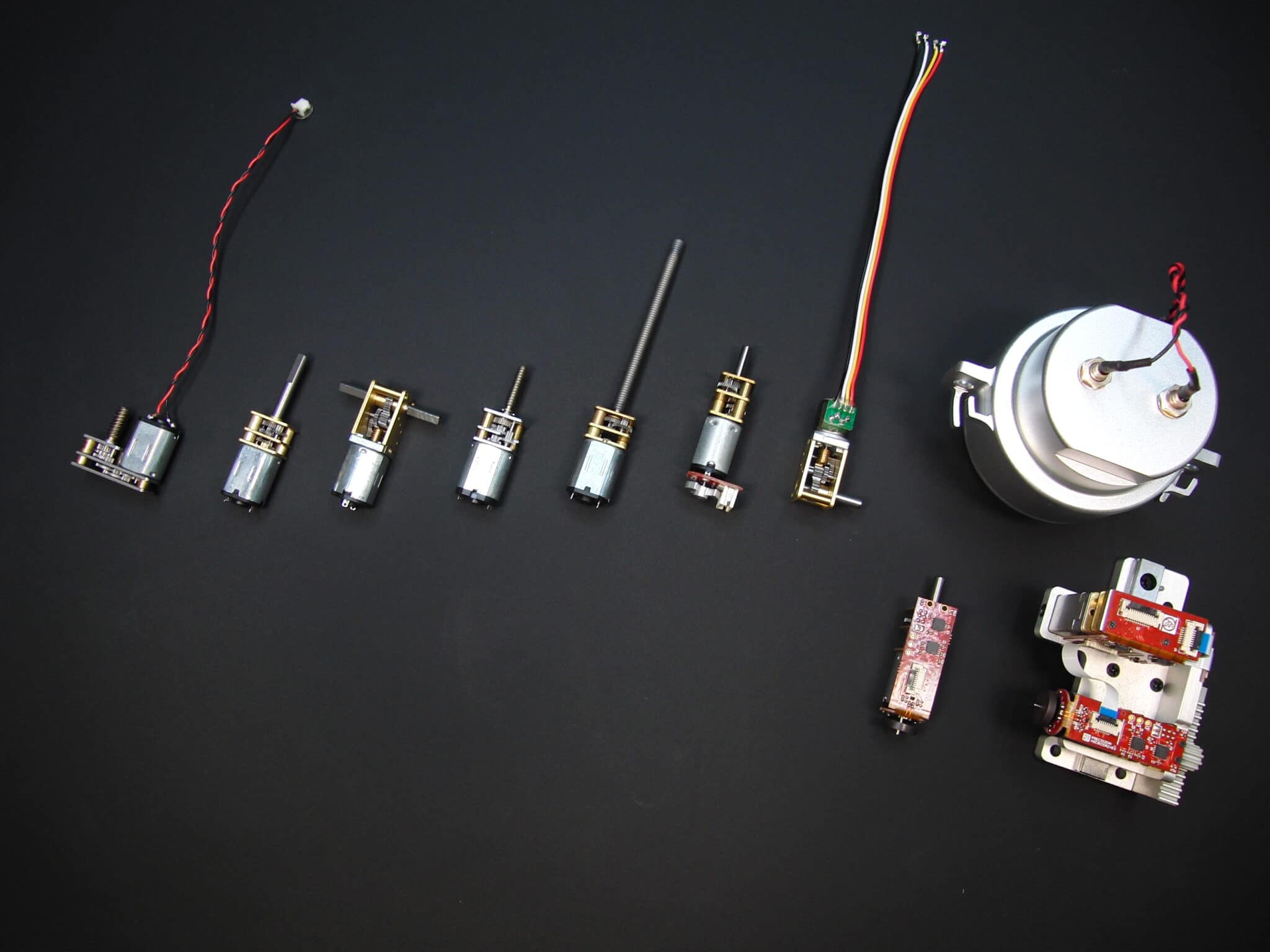
Brushless / DC motors and mechanisms
Designed and manufactured for your application
Precision Microdrives is a trusted international Brushless and DC motor specialist
Whether you need a miniature brushless or DC motor component, or a complex pre-assembled mechanism, our engineers put your application at the heart of every design.
We use our proven technology and processes to solve your motor and mechanism problems, reducing your costs, taking you from prototype to mass production.
We deliver a turnkey service to manage your motor and mechanism engineering risks delivering on time and to spec.
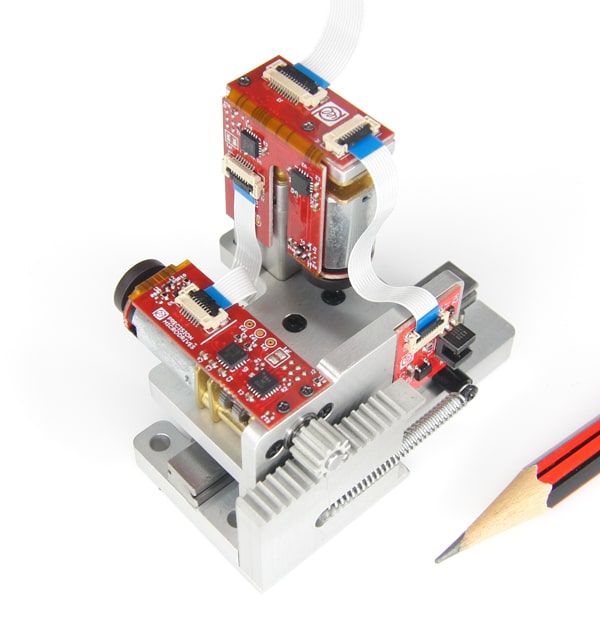
THE PRECISION MICRODRIVES ADVANTAGE
How can we help?
Custom assemblies
Longevity testing
Mechanism design
Engineering confidence
In-house production
Full testing validation
MOTORS AND MECHANISMS
Our products
From off the shelf motor components to fully validated and tested complex mechanisms, choose a motor and mechanism partner you can trust.
-
Brushless Motors
We offer a comprehensive range of DC brushless motors in both slotted and slotless (high torque and negligible cogging) designs, with matching gearboxes, commutation sensors, and encoders.
View Page
-
DC motors
Iron-core, coreless and brushless DC motor technologies in a wide range of form factors and sizes, with off the shelf sampling.
View Page
-
DC gear motors
Building on our range of DC motors, we integrate spur and planetary gearboxes, from 6mm to 60mm frame diameters.
View Page
-
Mechanisms
Custom motor assemblies designed and manufactured to your requirements. A turnkey service from design inputs to mass production.
View Page
-
Linear actuators
Precise, reliable and highly customisable linear actuators designed for a wide range of industrial, commercial and medical applications.
View Page
-
Vibration motors
With every vibration and haptic technology covered, we’ll help you select the best vibrating solution for your application.
View Page
WHY PMD?
Where we add value
OPTIMISED DESIGN
Motor and mechanism design for your application
Design is at the heart of what we do at Precision Microdrives.
We design to your specifications based on your exact application requirements with consistency, quality and efficiency.
We understand the technical and manufacturing challenges motors present and enjoy providing solutions. Through our design we reduce costs and engineering risk, leading to innovative solutions delivered on time and to spec.
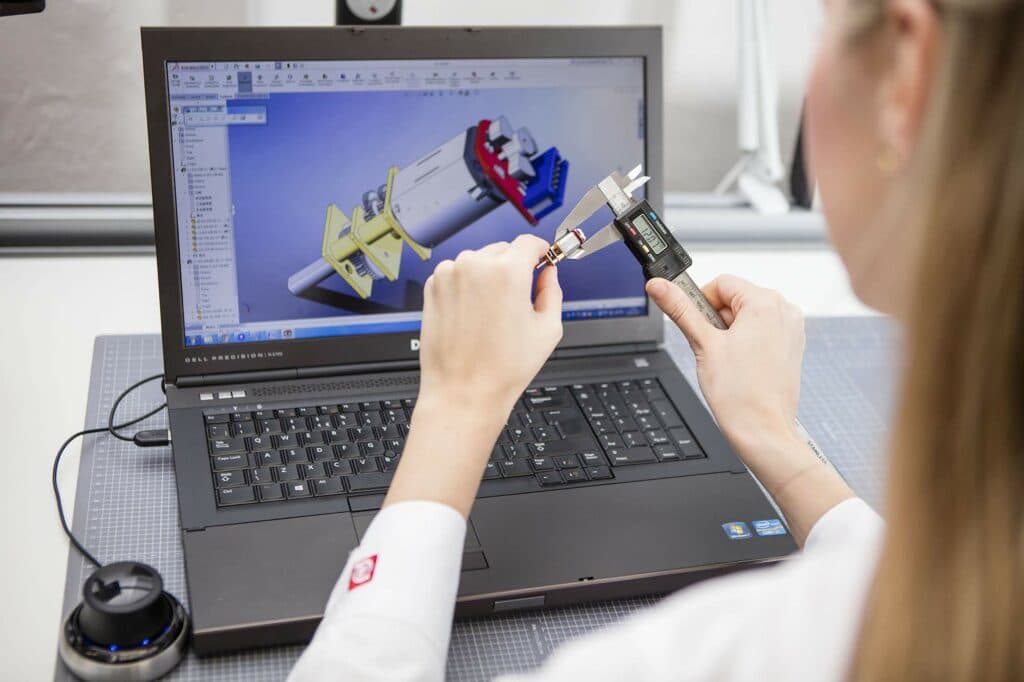
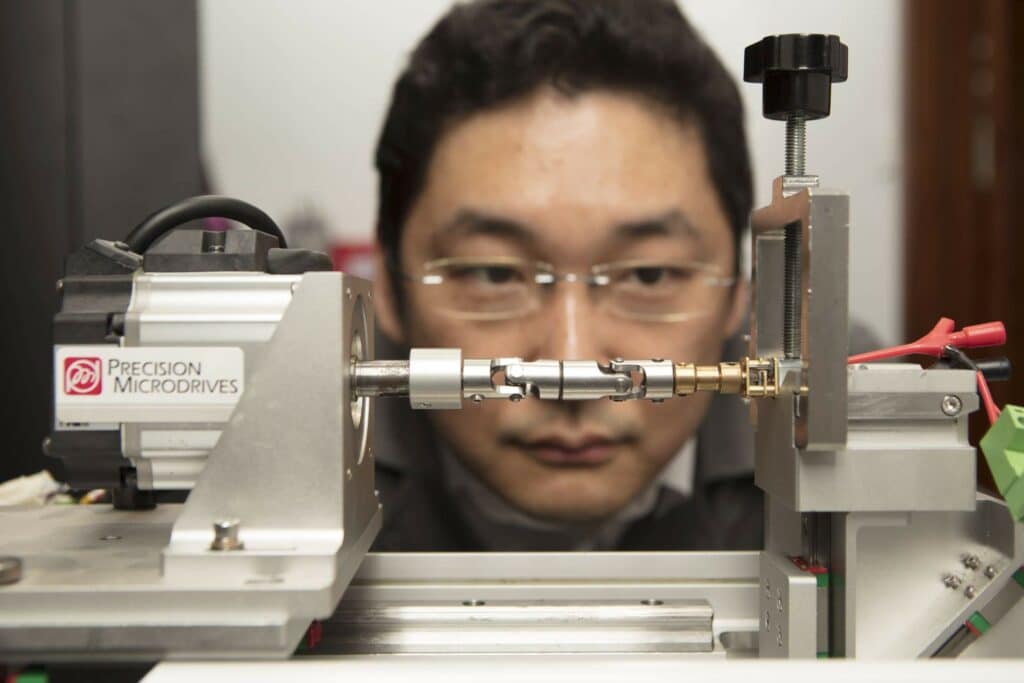
INNOVATIVE TECHNOLOGY
Technical expertise to manage your risk
It’s our motor engineering expertise combined with our commitment to technical diligence, that makes Precision Microdrives a design and manufacturing partner that you can trust.
We offer you the know-how, processes, experience and infrastructure to allow us to overcome the technical challenges that come with designing and manufacturing durable miniature motors and mechanisms.
Let us add value to your next project.
QUALITY CONTROL
Precision processes
We are proud to say we are a BSI ISO 9001 trusted designer and manufacturer of motors and mechanisms.
Therefore it is unsurprising that our business holds a dedication to controlling quality so that we can deliver consistently manufactured motors and mechanisms from one batch to the next.
It helps that among our engineering teams there is a common fascination in dynamic metrology and motor dynamometer techniques, but the real heroes are the quality control engineers and the mature quality processes that they operate.
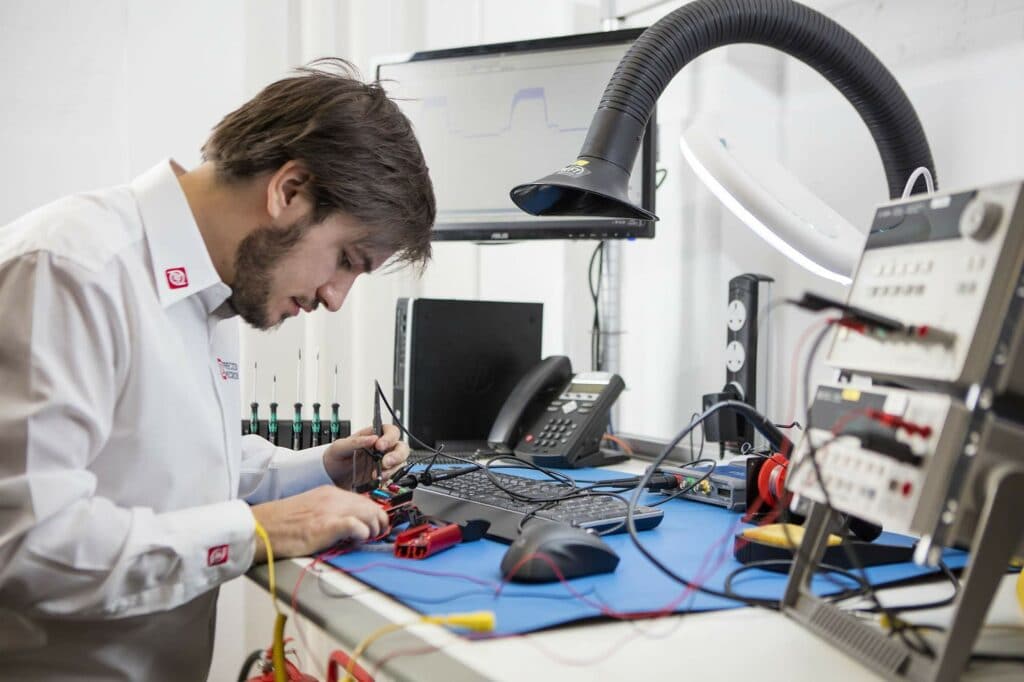
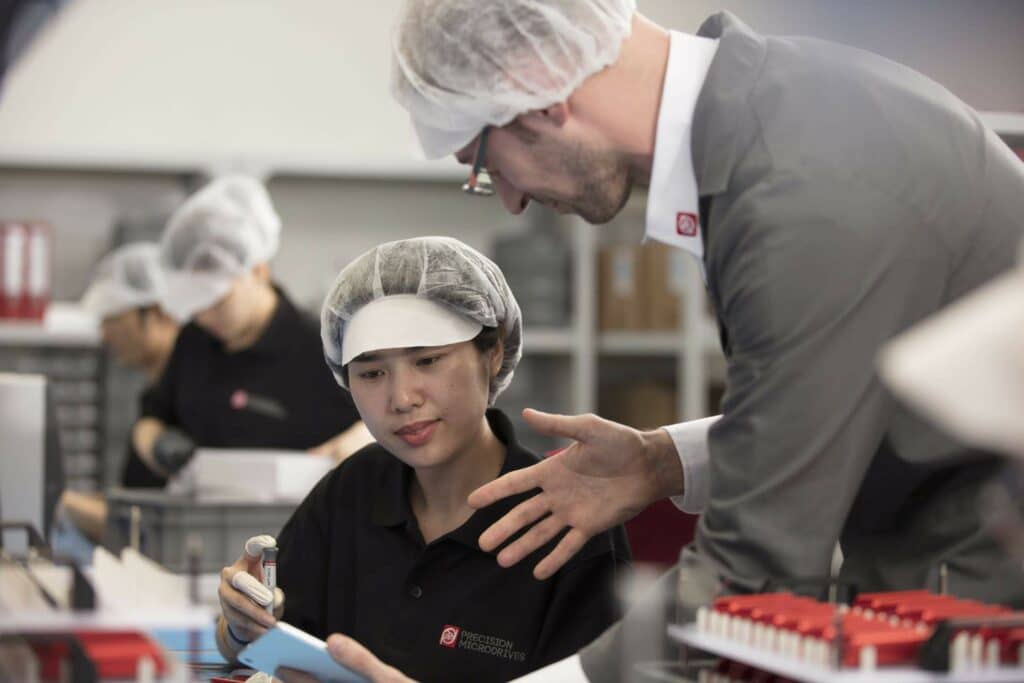
INTERNATIONAL MULTI-LINGUAL TEAM
Precision Microdrives partnership
Our company culture is built around fostering long-term partnerships building trust and confidence. We strive to have honest, open communication and our vision is to add as much value as we can during the partnership.
Our international, multi-lingual team combines technical expertise with exceptional customer service and will often deal with you in your native language and time zone. This will ensure there are no cultural misunderstandings. We don’t just provide a solution and walk away. You will receive our continued support throughout the whole project lifecycle.
HIGH QUALITY RELIABLE MOTORS & MECHANISMS
Industries we serve
Designing mechanisms for a wide range of medical, industrial and consumer applications.
PRECISION PROCESSES
Our capabilities
We can support you through the whole journey from prototype to high volume cost-effective mass production:
Discover more
Resources and guides
Discover our product application notes, design guides, news and case studies.
Case studies
Explore our collection of case studies, examples of our products in a range of applications.
Precision Microdrives
Whether you need a motor component, or a fully validated and tested complex mechanism – we’re here to help. Find out more about our company.